Helpful tips for scenarios involving inventory discrepancies, compliance reporting and products
How do I audit products that need to be returned or destroyed?
-
Login into your dashboard
-
Go to Inventory > Overview
-
Find the product and click on the quantity on the far right column
-
Select "- Remove" then select "Return" or "Destroyed"
-
Put in the notes "product needs to be returned to the vendor." or "product needs to be physically destroyed".
-2.png?width=590&height=470&name=image%20(17)-2.png)
Why am I getting negative inventory amounts in my audits while sales are happening?
You may see negative inventory quantities while performing an audit during your business hours because you did not refresh the latest "expected" inventory quantities.
The expected amount can be refreshed but not the counted amount. The person doing the audit would have to manually remove the item that they just sold from the counted column in the audit or recount it as the number that you counted would also be affected by the units you sold. The reason for this is that GL can't update a user field for them.
-2.png?width=262&height=50&name=image%20(18)-2.png)
For example:
You performed an audit for the following product: 7Acres - Jack Haze - 7g and as a result there was a negative inventory of -7 units.
-
The audit was created on "Apr 22, 2021 4:24 pm"
-
At this time, there were 15 inventory units of the 7Acres - Jack Haze - 7g.
-
The audit was completed at "Apr 22, 2021 9:10 pm"
-
At this time, there were 4 inventory units of the 7Acres - Jack Haze - 7g.
Because the audit started with 15 units and you only counted 4 units, the audit reduced 11 of those units in the inventory resulting in the quantity of -7.
A way to avoid this problem in the future is to make sure that you are clicking the refresh button on your audit prior to marking it complete.
This will update the expected quantities and show you the time and date that the inventory was refreshed. As a result will update the expected inventory count accordingly. You'll want to make sure it is up to date to correspond with the active inventory and not the inventory that was available upon creating the audit.
How often should you audit?
Most stores will want to do an inventory count at least once a week. Twice if possible.
Especially new stores with new staff. Frequent audits can help you avoid running into issues that are harder to fix as time passes and ensures best practices for product handling and product familiarity.
Stores will also want to perform an audit at the end of the month before running their compliance reports. This is because any audits that happen after 12:00AM on the first will not affect the previous month.
If you notice a product that has been sold incorrectly than we recommend correcting that right away using the Inventory Adjustment in Inventory Overview.
What should I do when products are recalled? (Alberta)
You can subtract the inventory from the system and make a note that it is due to a recall.
-
Go to Inventory> Overview> Find the recalled product
-
Remove the unit(s) from the inventory
-
Select the reason ("Return")
-
Select the lot number (if the product has a lot tracking enabled)
-
Include any relevant notes
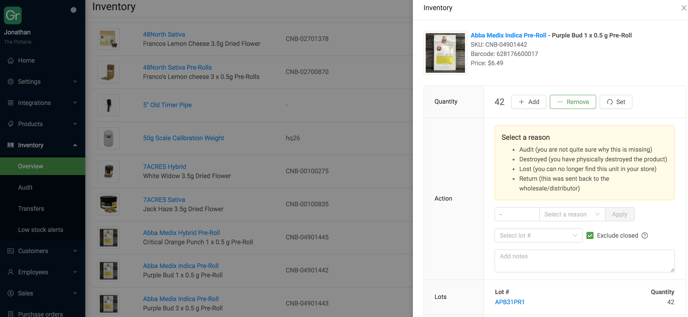
How do I export and import .csv file transfers?
To import into a transfer the .csv file can only contain the SKU and quantity.
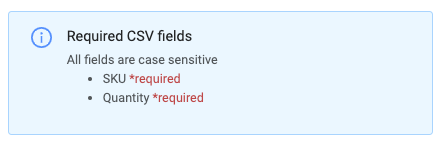
When you export transfers from Greenline they look like this.

But need to look like this to be imported.
Tracking Products Explained
"Track" does not relate to compliance, it means that the item is countable in Greenline.
An example of when to use "Don't Track" would be for delivery fee where you don't have stock in that "product" and you can never run out of it in inventory as it is a service.
Only Tracked items appear in inventory.
How to set up low stock alerts
-
Go to Inventory> Overview> Select "Low stock level" from the "Table columns" filter
-
You will see under each of your products' quantities a "Low" tag to indicate if a low stock quantity was set.
-
To set low stock quantities, click on the quantity to expand more details, enter in the low stock quantity for each of your products
-
Once you've set up your low stock levels, go to Inventory> Low Stock Alerts > Add alert >
-
Whatever user is logged in that set the alert will now receive an email when the low stock alert is triggered